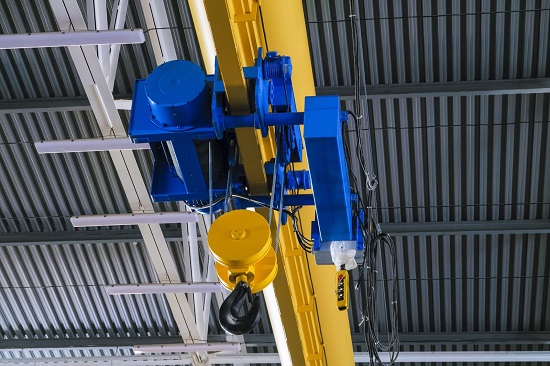
Having a proactive and customized overhead crane inspection and preventive maintenance program is essential to workplace safety and productivity. This article aims to answer frequently asked questions on overhead crane and hoist inspection, repair, and maintenance.
Q: Why is it important to have an overhead crane inspection and preventive maintenance plan in place?
A: Having regular inspections and preventive maintenance activities helps identify potential risk areas and reduces downtime while supporting compliance requirements. Moreover, keeping overhead crane and hoist systems safe for daily use is a more cost-efficient option to lawsuits, medical expenses, and the tedious administrative work related to finding a replacement for an injured employee.
Q: How often should overhead crane and hoist systems be inspected?
A: Routine overhead crane and hoist inspections are a must regardless of their condition because of the work they complete (i.e., lifting loads in varying sizes and weights). There are four inspection categories: Initial, Functional, Frequent, and Periodic.
The initial inspection is conducted after the installation of a new crane or hoist, or after the equipment has been reinstalled after alteration, modification, or repair.
Functional inspections must be done before every shift.
Frequent inspections should include all aspects of the functional inspection, paying extra attention to the hoist brake, wire rope, and load chain. The inspector must be on the lookout for any unusual sounds. The hook and latch must be inspected as well. A crane that operates under “normal service” should be inspected monthly; a crane in “heavy service” should be inspected weekly to monthly, and a crane in “severe service” should be inspected daily to weekly.
Under periodic inspections, cranes used for “normal service” and “heavy service” should be inspected yearly while cranes in “severe service” should be inspected quarterly.
Q: How do you inspect an overhead crane?
A: Check crane and hoist components for signs of malfunction, deterioration, and everyday wear and tear. Functional operating mechanisms, hydraulic and air system components, and crane hooks must be inspected daily, before starting each shift.
- Functional operating mechanisms – Check for maladjustment
- Hydraulic and air system components – Inspect valves, lines, tanks, drain pumps, and other components for deterioration or deficiency
- Crane hooks – Check for cracks and signs of deformation.
Inspect rope and end connections as well as hoist chains and end connections every month.
- Rope and end connections – Check broken strands or signs of wear and tear
- Hoist chains and end connections – Are there signs of distortion or anything else that might hinder it from functioning properly?
All findings must be documented in detail so you can have an accurate record of the overhead crane’s maintenance history.
Q: What’s the difference between corrective and preventive maintenance?
A: Corrective maintenance is done when there is equipment failure or malfunction. Examples of corrective maintenance procedures include retrofits and customizations.
Preventive maintenance, on the other hand, involves taking the necessary precautions to prevent accidents or equipment failures even before these happen.
You’ll need to do both at some point. Integrity Crane and Hoist recommends having a highly trained team of professionals to complete these tasks.
Working out of Columbia, Tennessee, Integrity Crane and Hoist is a full-service overhead crane and hoisting equipment company that designs, engineers, manufactures, installs, modifies, modernizes, and load tests industrial bridge cranes, gantry cranes, ergonomic workstations, runway systems, monorails, power systems, and control panels. They also perform inspections, repairs, and preventative maintenance for all types and brands of cranes, hoists, vacuum filters, and below-the-hook lifting devices. Get in touch today to learn more.
Call Integrity Crane and Hoist at (615) 302-3431 for more information.